Customer Goals
Increase
storage density.
Accelerate
picking speed for small parts.
Minimize
unneccessary walking.
Ensure
on-time project completion.

With this being a greenfield facility, our customer had many options, allowing our team to maximize the design to fit their unique needs. As a fulfillment center for aftermarket aerospace parts, they have up to 20,000 small parts on hand. The ability to receive and ship these parts quickly and in an organized fashion was vital to ensure the facility operated at its highest efficiency.
A few key benefits of VLMs drove the step forward in efficiency for our customer. Valuable floor space was saved by utilizing vertical air space, freeing up areas to be used for receiving and packing shipments. Order accuracy and picking speed will also increase and can be attributed to the put-to-light technology utilized, ultimately leading to higher throughput and happier customers.
Collaboration with a trusted third-party installer and our in-house project manager ensured meticulous attention to detail and seamless communication throughout the project. Our in-house project coordinators, CAD team, engineers, and logistics team also played integral roles to ensure the project was successful.
The Results
3
Modula Vertical Lift Modules
storing 3,000 cubic feet of small parts
20,000
Product Locations within the Selective Racking
5
Power Mobile Carts
Also,
Work Desks, Line Striping, Rack Labels, Drivers Cages
Final Thoughts

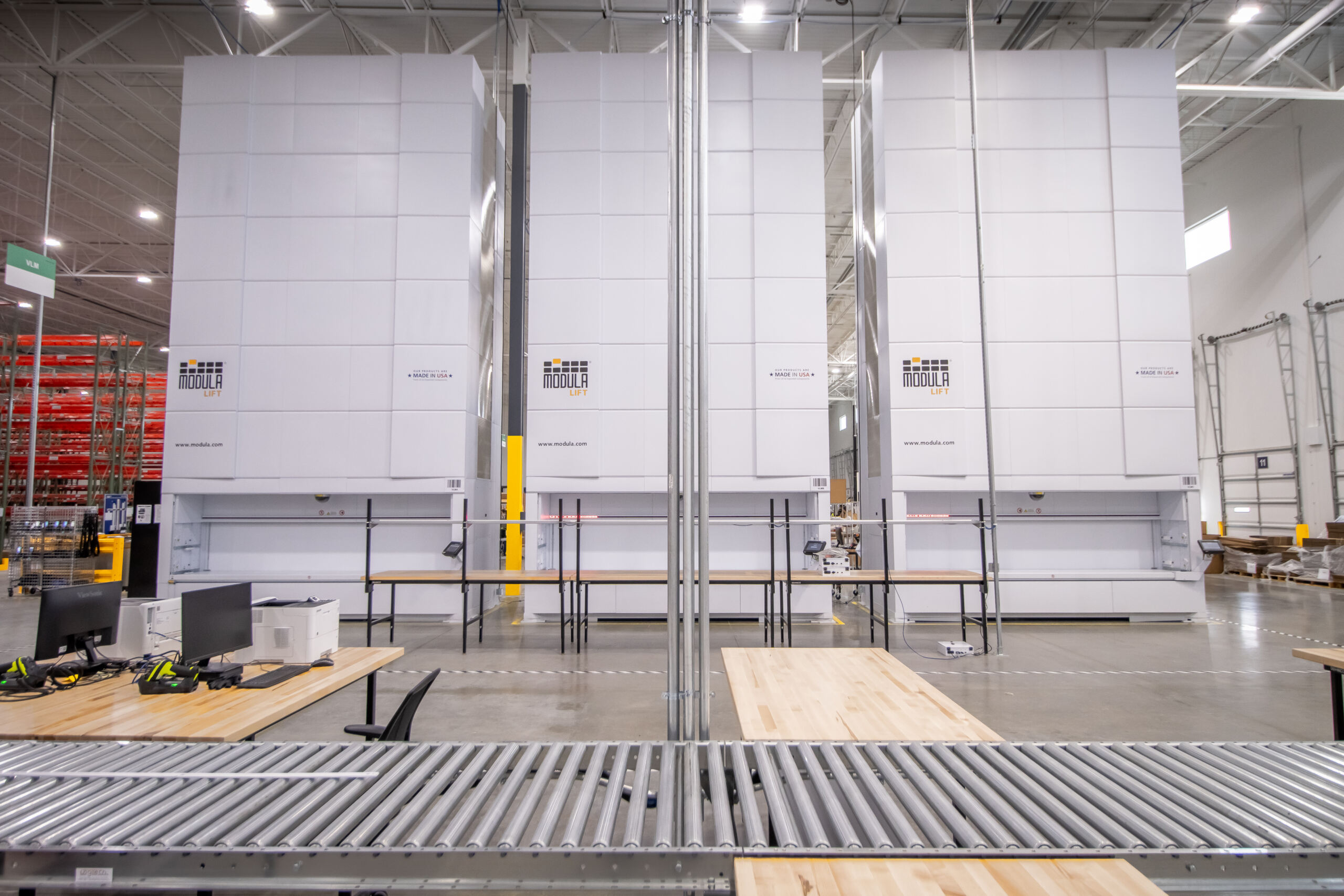





















