A retail/e-commerce enterprise was in the process of building a new facility to consolidate its operations and house its retail storefront. In this new facility, they aimed to revamp their processes by implementing diverse automation measures to increase productivity through reduced employee dead time. With over 800,000 unique products being processed and sold by this company annually, these new solutions were necessary to improve efficiency in their daily operations. To ensure a smooth transition between the facilities, Storage Solutions was engaged to refine, execute, and complete the design of the existing facility.
Customer Goals
Reduce
employee dead time and implement automated tasks.
Consolidate
multiple facilities into one.
Tailor
a solution unique to the customers needs.
Our customer had already developed an initial facility design, but they looked to Storage Solution’s real-world expertise and practical knowledge to guide and implement the final design, installation, and engineering, primarily in regard to the conveyor system. Leveraging our experience with the automation solutions utilized and the background of our team members who have previously worked in similar warehouse environments, we were able to offer the best possible solution to meet the customer’s unique requirements.
The Results
Over four to six weeks, we collaborated with the customer to evaluate the existing plans and ensure alignment with their goals. Following the initial consultation, our team spent eight weeks on the detailed engineering piece of the project. Once our team finalized the comprehensive warehouse design, we engaged multiple trusted partners to deliver optimal solutions for both the storage and dynamic requirements.
A crucial aspect of the project was coordinating our installation activities with the general contractor responsible for the building project. Given the vast expanse of the 600,000 sq. ft. facility, it was essential to sequence the installation in various areas. We utilized our in-house engineering and controls team to install and implement the conveyor system while engaging a reputable third-party crew for the pallet racking installation.
Our in-house project management team was pivotal in maintaining order and facilitating clear communication among all parties involved throughout the seven month long mechanical/electrical installation phase. From day one, our project management team helped to foresee potential project hurdles and seamlessly execute each step of the project with those in mind.
We additionally installed 1 strip belt sorter and 2 wide belt sorters.
3+
miles of conveyor installed.
20k
pallet positions of racking installed.
3
Cognex scanners installed.
Final Thoughts
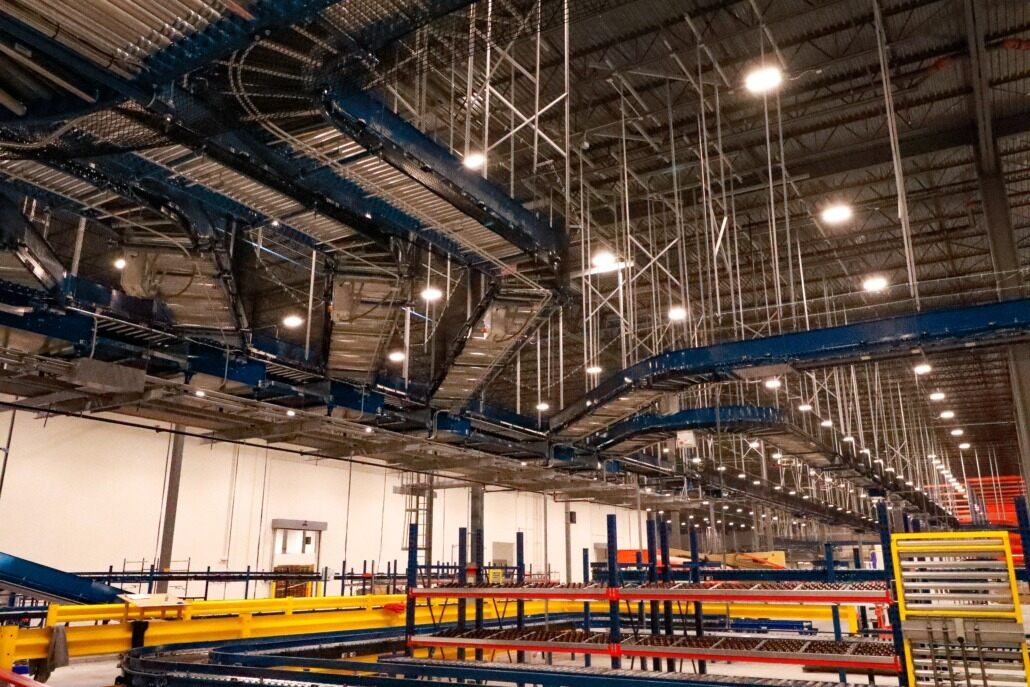
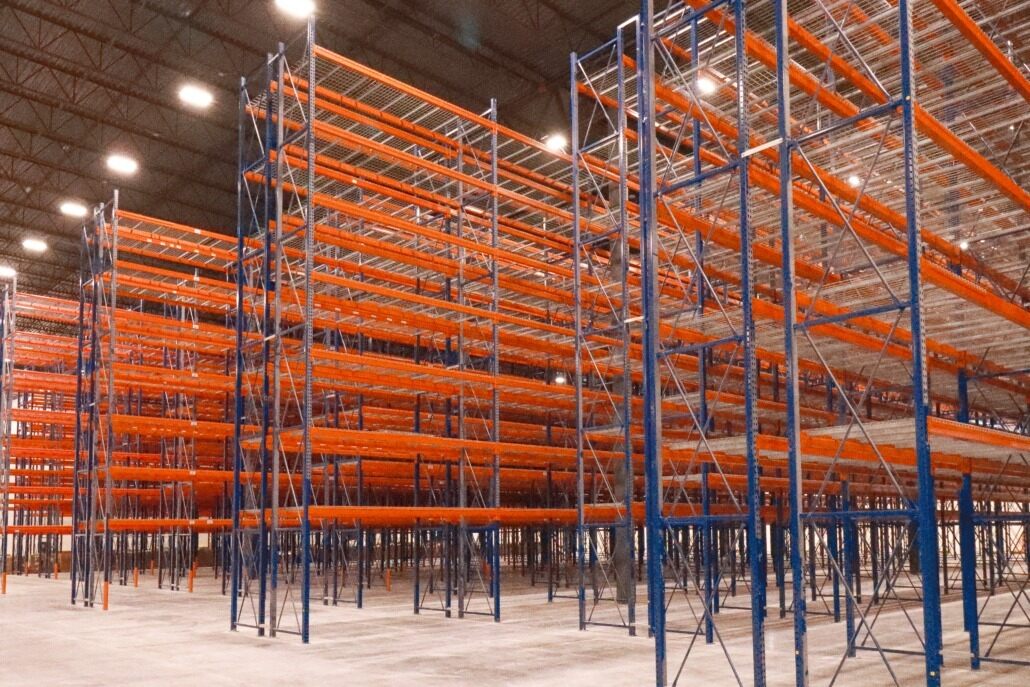
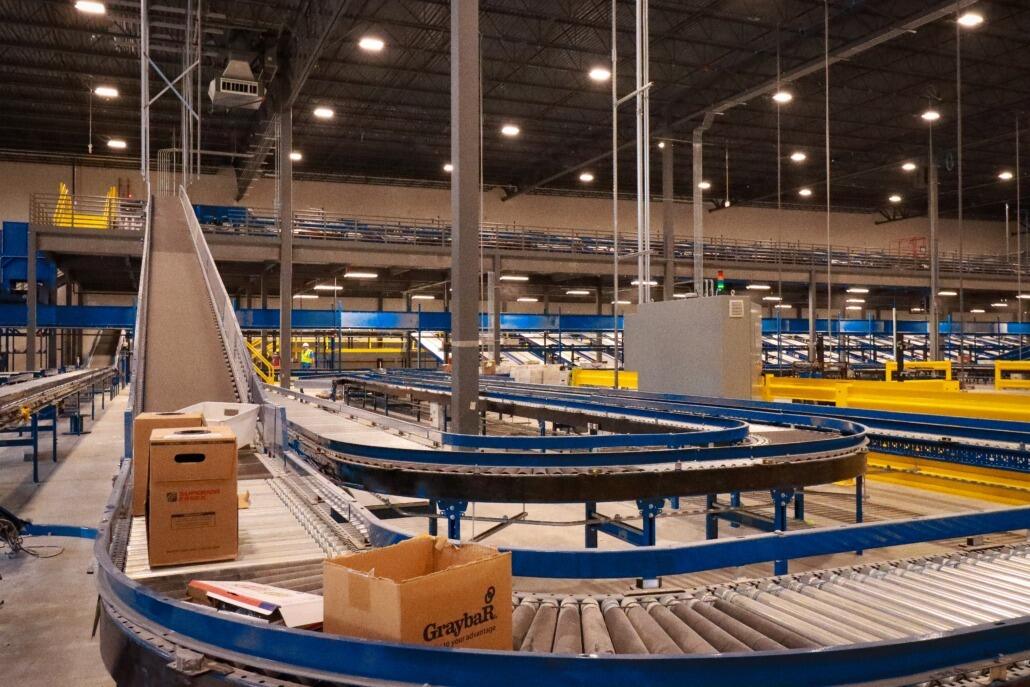
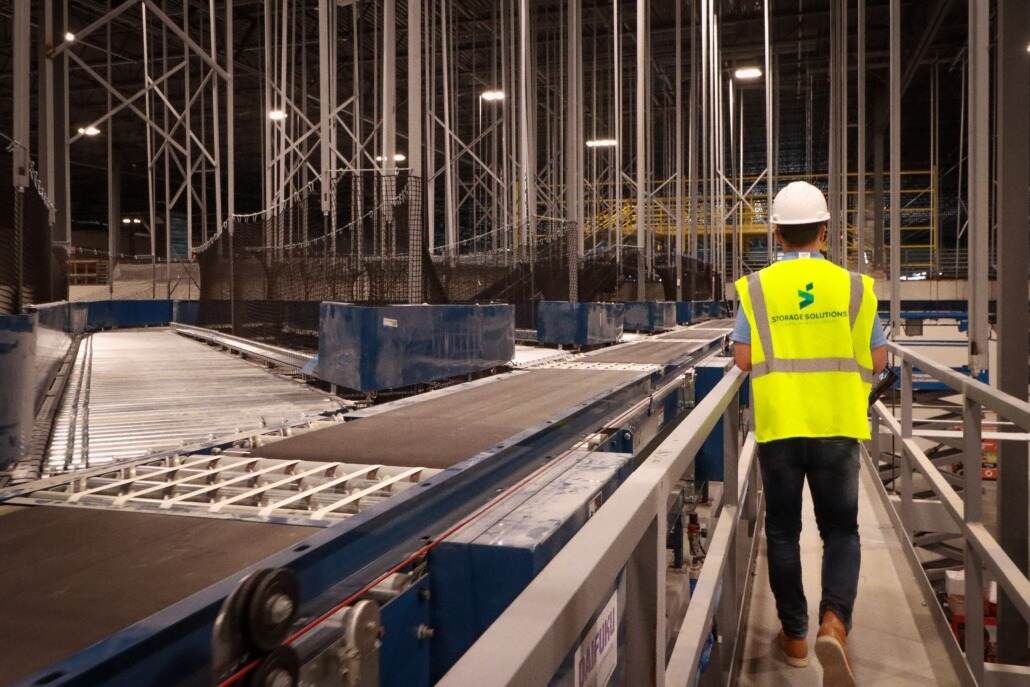

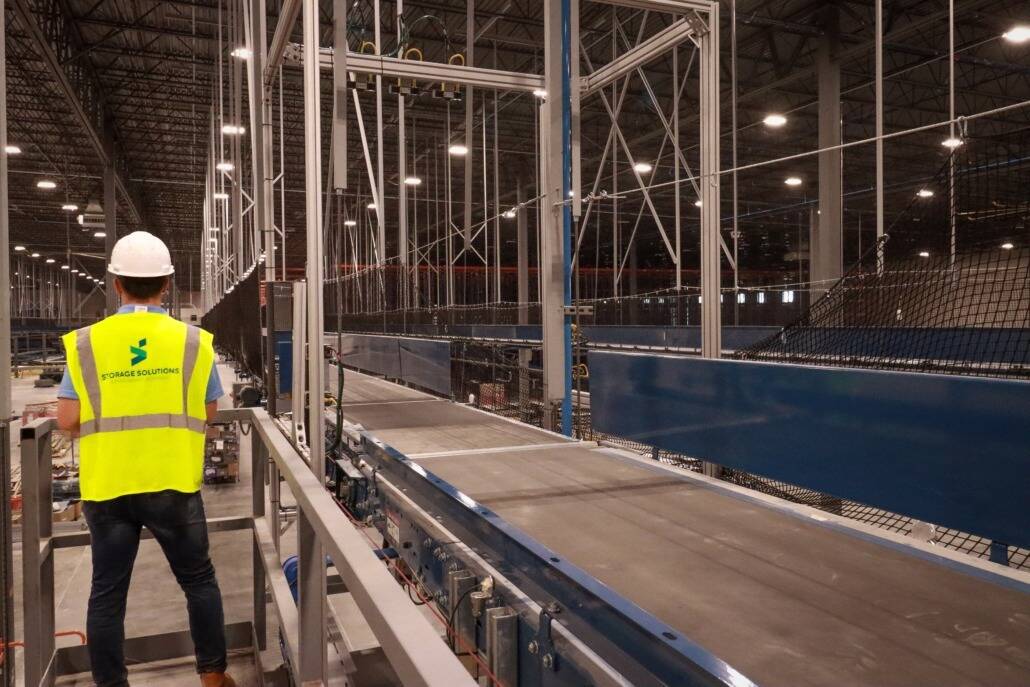
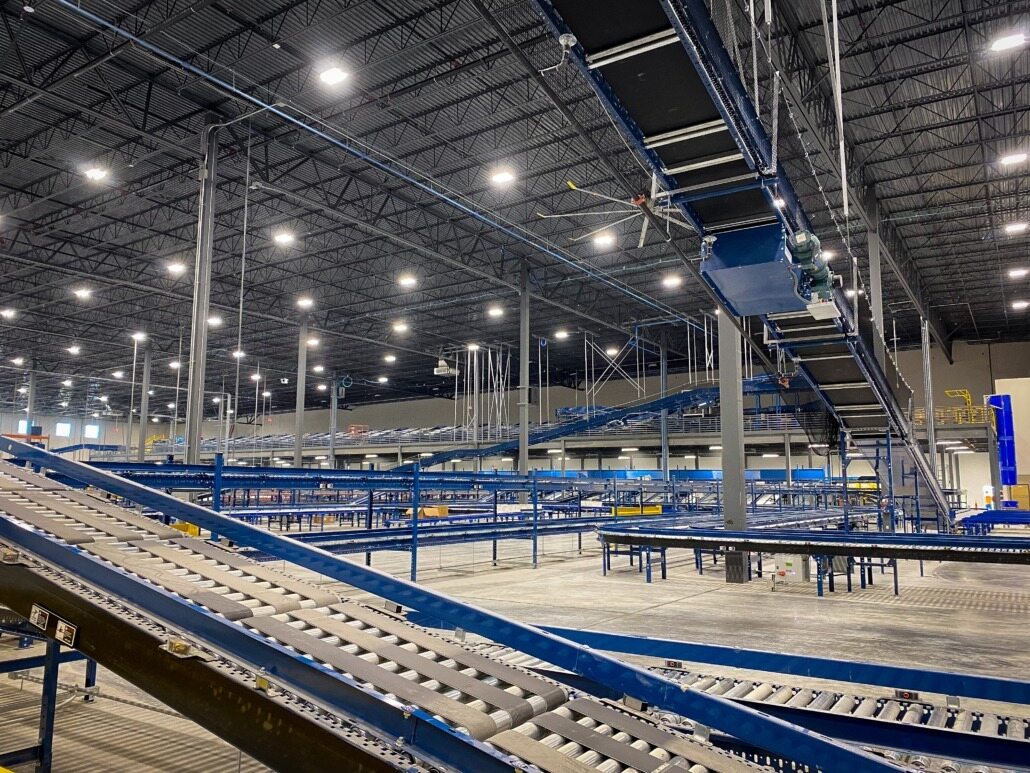
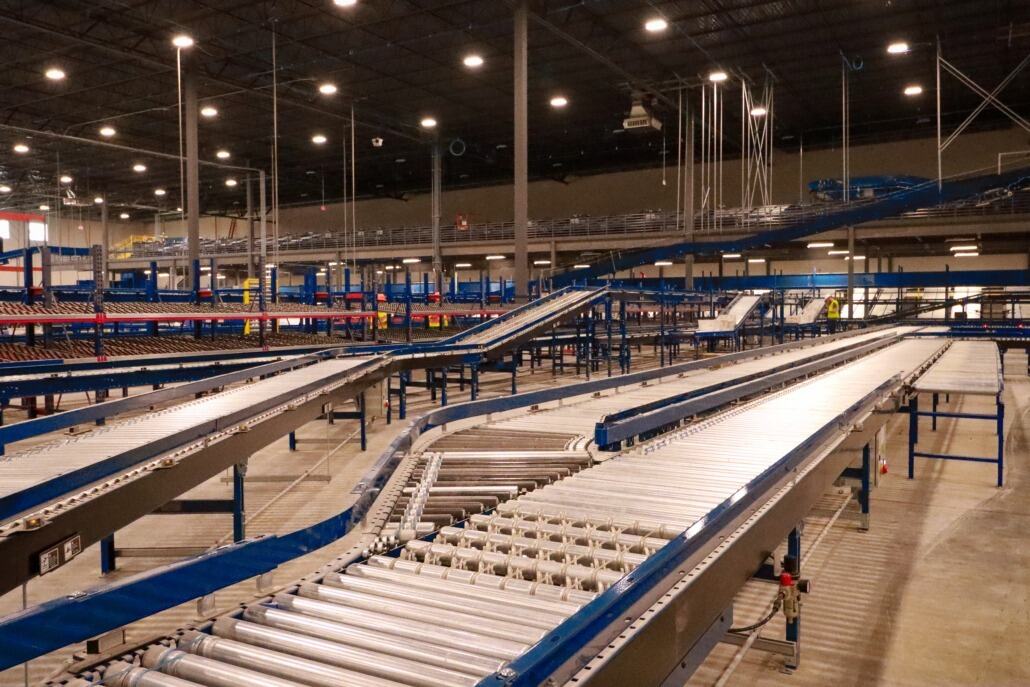
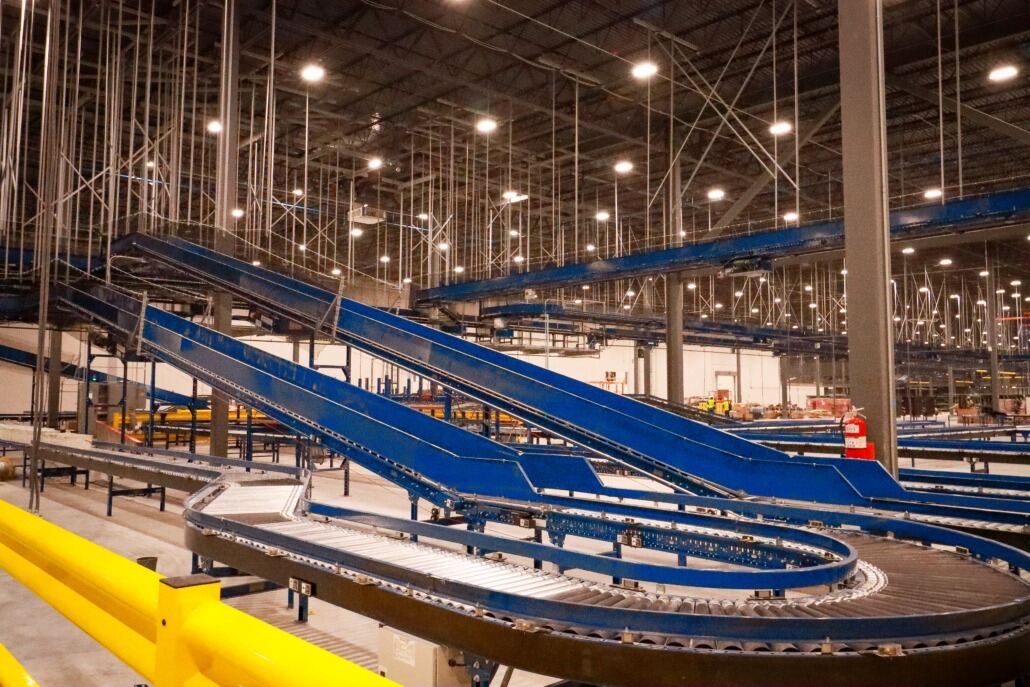
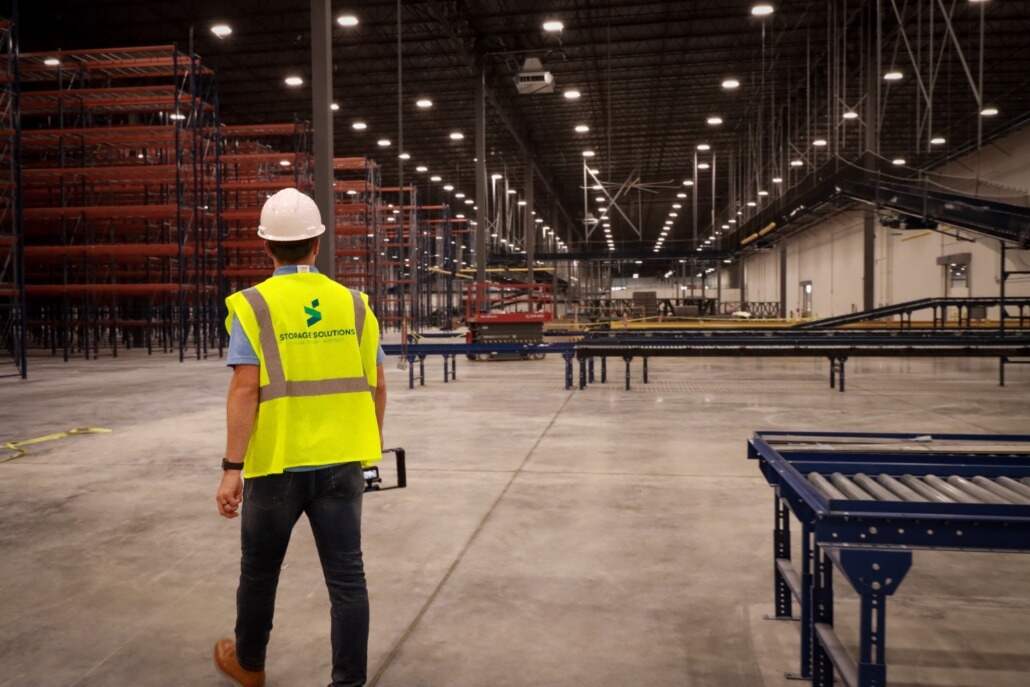
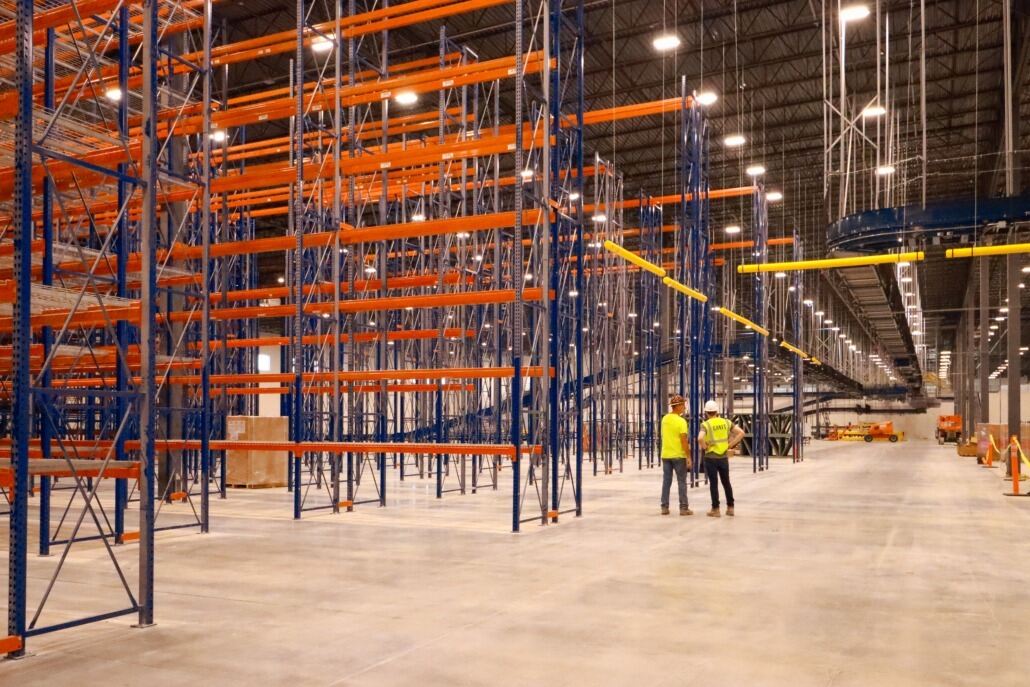
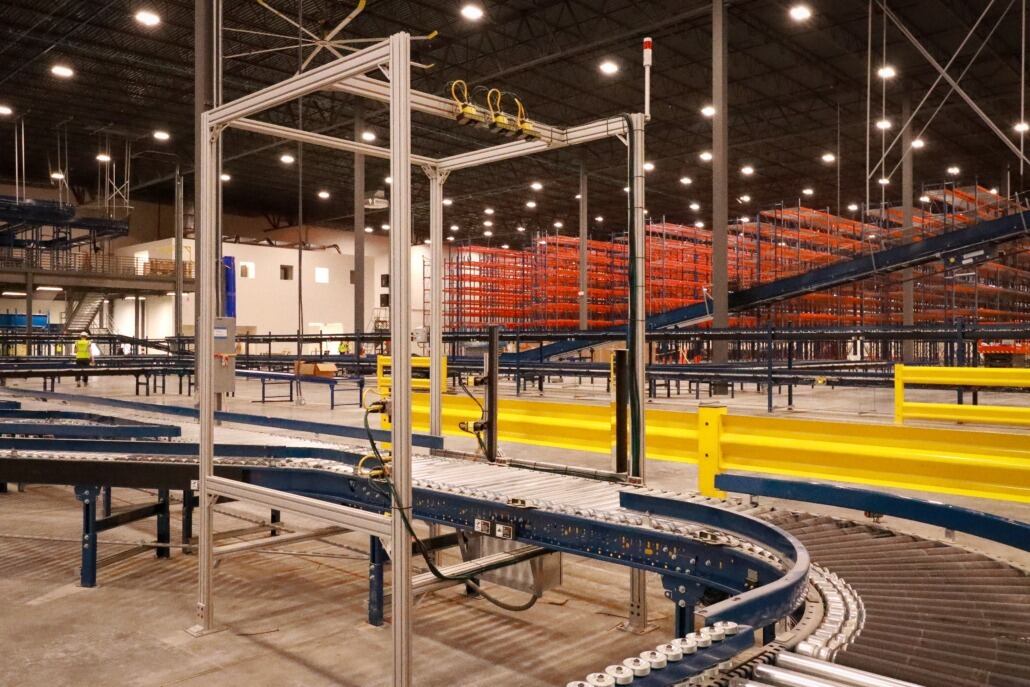
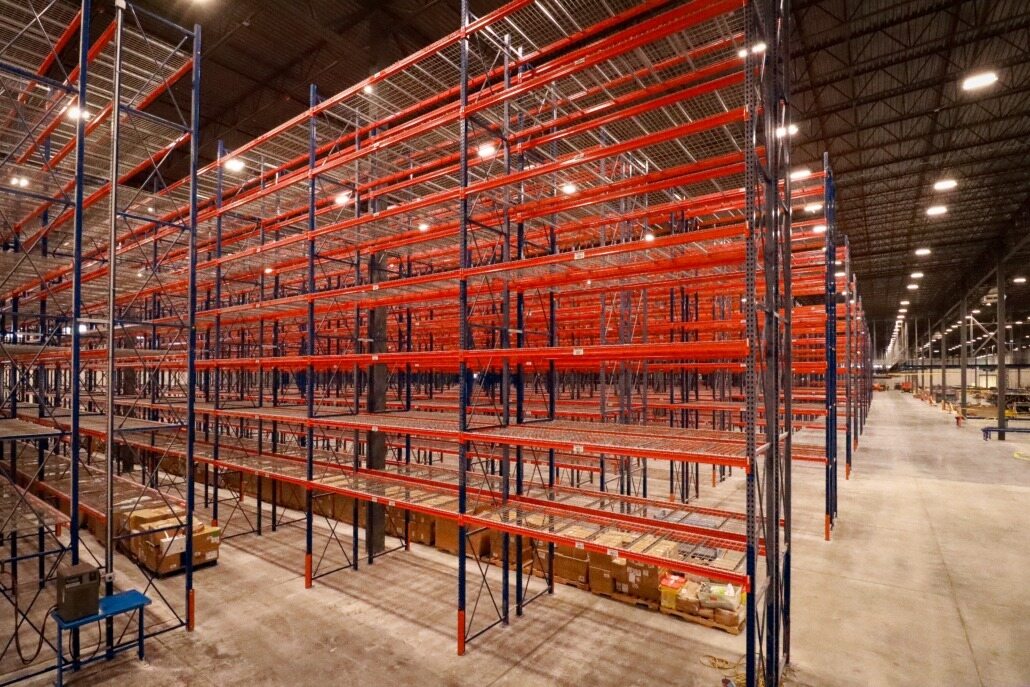
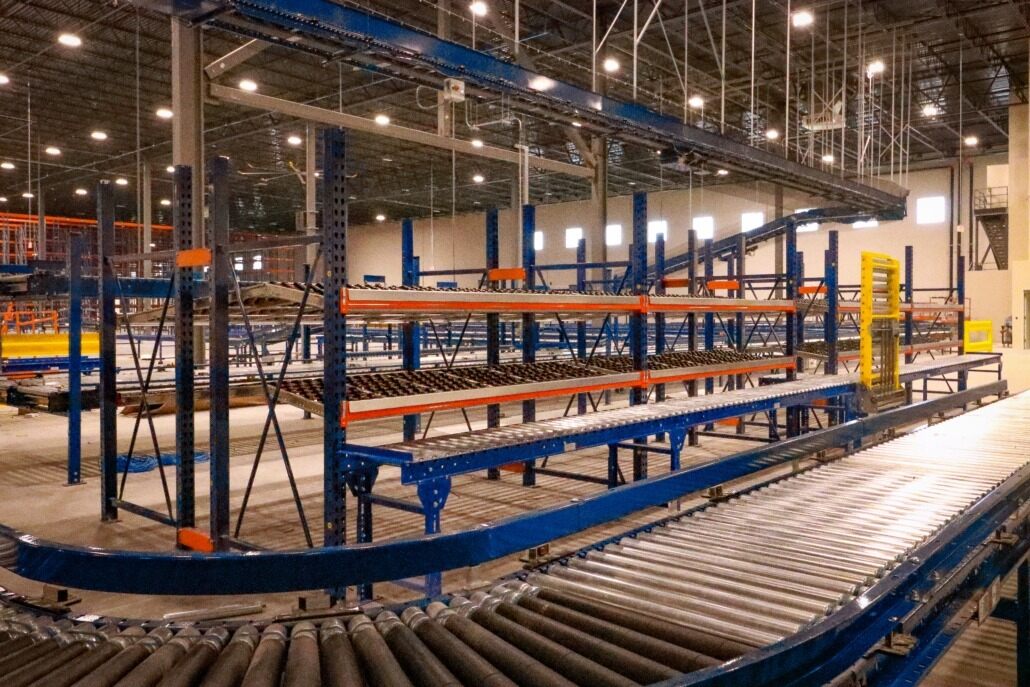
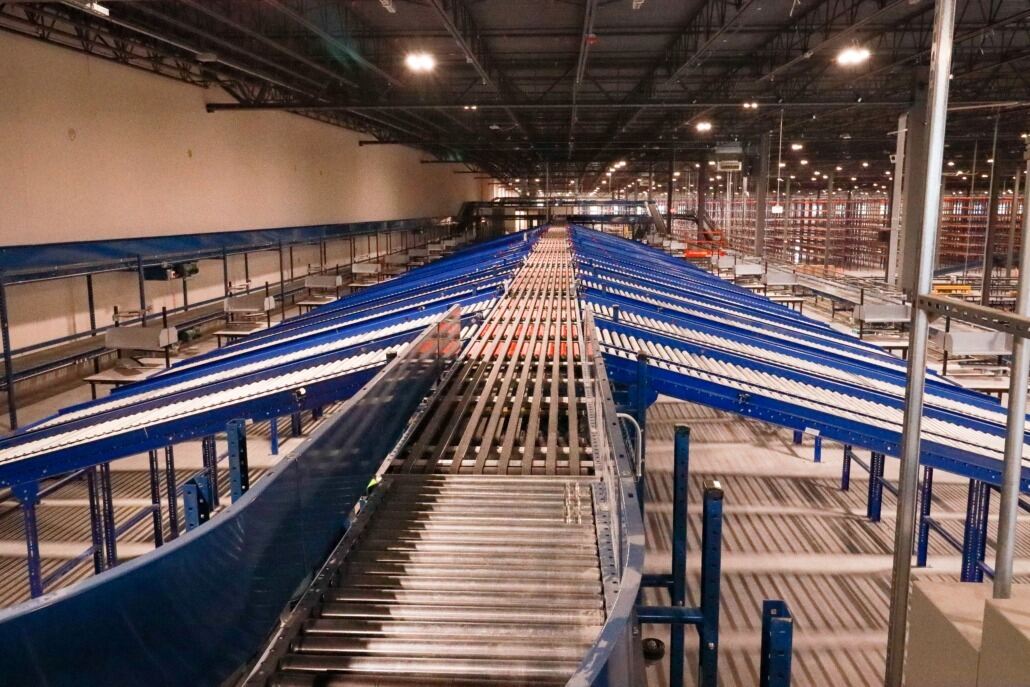
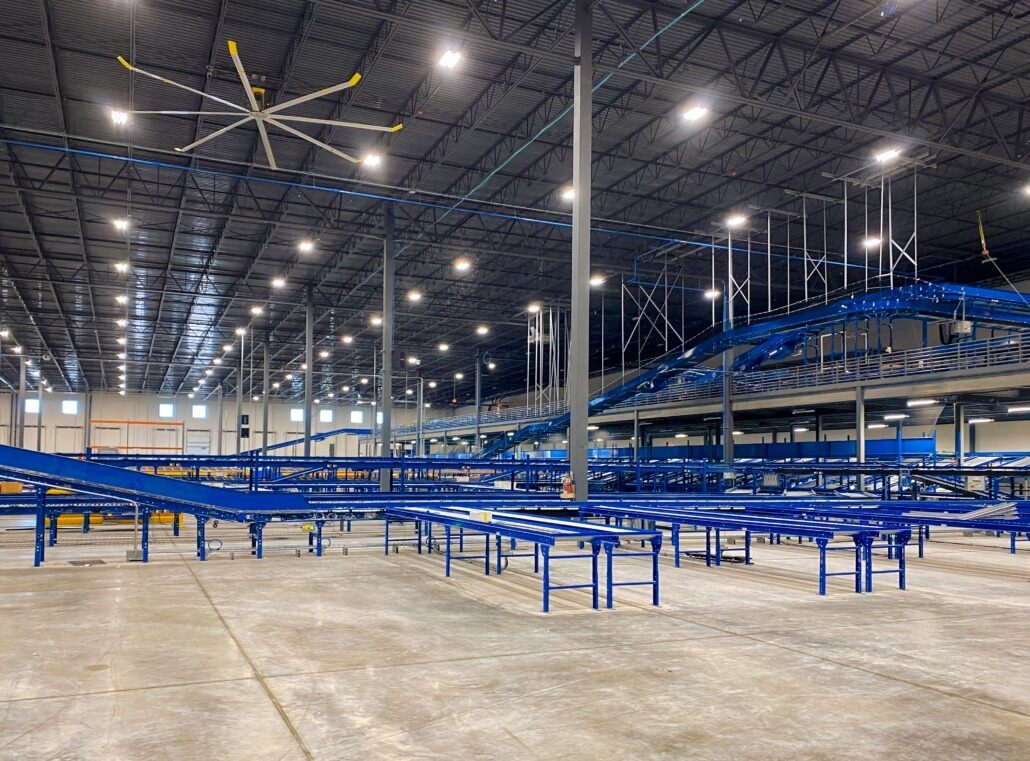