Customer Goals
Understand
their operation's current and future storage needs.
Improve
storage and become more operationally efficient.
Maximize
space in the new facility.
Our client’s most significant pain point was understanding how best to solve their need for efficiently moving products while still maximizing the facility’s storage with a new product line. Although the client did not have all the data necessary for a complete analysis, our Solutions Engineering team was able to use real-world operations experience and industry knowledge to fill in the gaps.
While developing a project roadmap, our Solutions Engineering and National Accounts teams enlisted our partners to provide options, including a mix of storage and dynamic solutions, with a plan to achieve a financial return from these capital expenditures. For this project, the options included VNA single selective rack, dense storage, pallet shuttles, and automated storage and retrieval systems (AS/RS). We also provided estimates on equipment and labor installation time and how alternate layouts could affect their future labor costs with additional throughput.

The Results
Our client’s most significant pain point was understanding how best to solve their need for efficiently moving products while still maximizing the facility’s storage with a new product line. Although the client did not have all the data necessary for a complete analysis, our Solutions Engineering team was able to use real-world operations experience and industry knowledge to fill in the gaps.
While developing a project roadmap, our Solutions Engineering and National Accounts teams enlisted our partners to provide options, including a mix of storage and dynamic solutions, with a plan to achieve a financial return from these capital expenditures. For this project, the options included VNA single selective rack, dense storage, pallet shuttles, and automated storage and retrieval systems (AS/RS). We also provided estimates on equipment and labor installation time and how alternate layouts could affect their future labor costs with additional throughput.
46k
pallets stored in a 110 pallet-deep shuttle storage system.
6400
pallet positions in very-narrow aisle (VNA) racking.
5000
pallet positions of floor stacking.
$625k
estimated in savings per year.
Final Thoughts

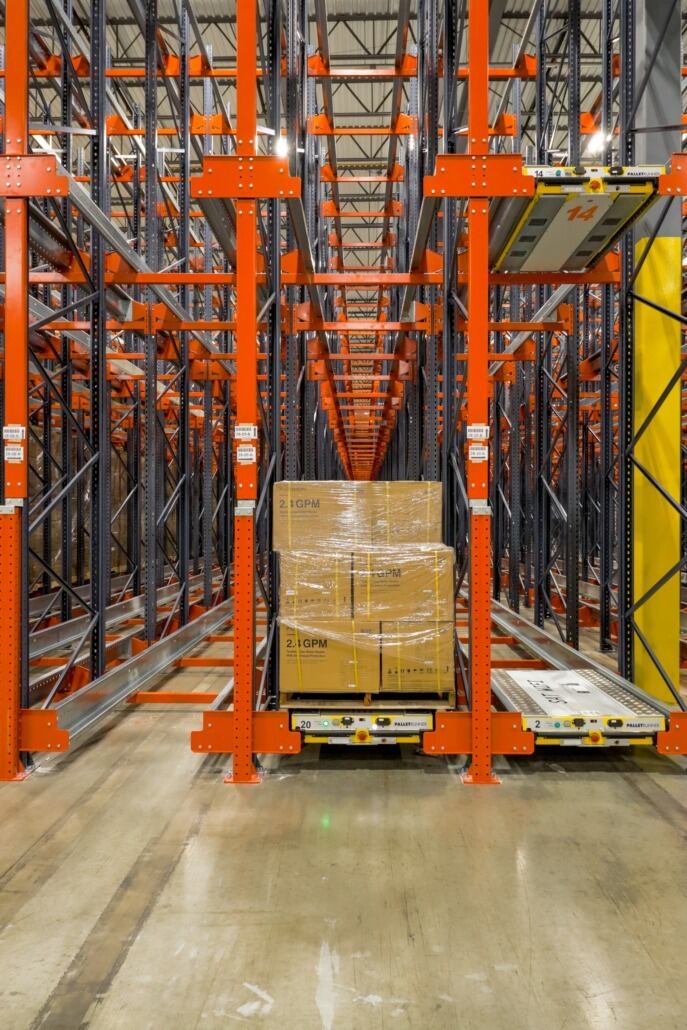
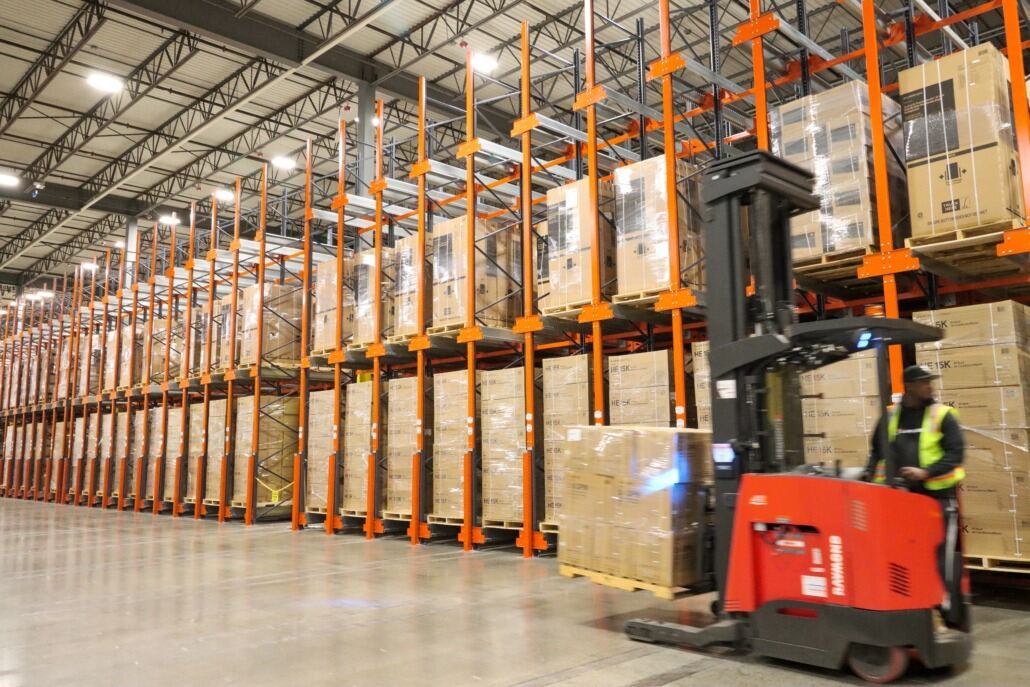



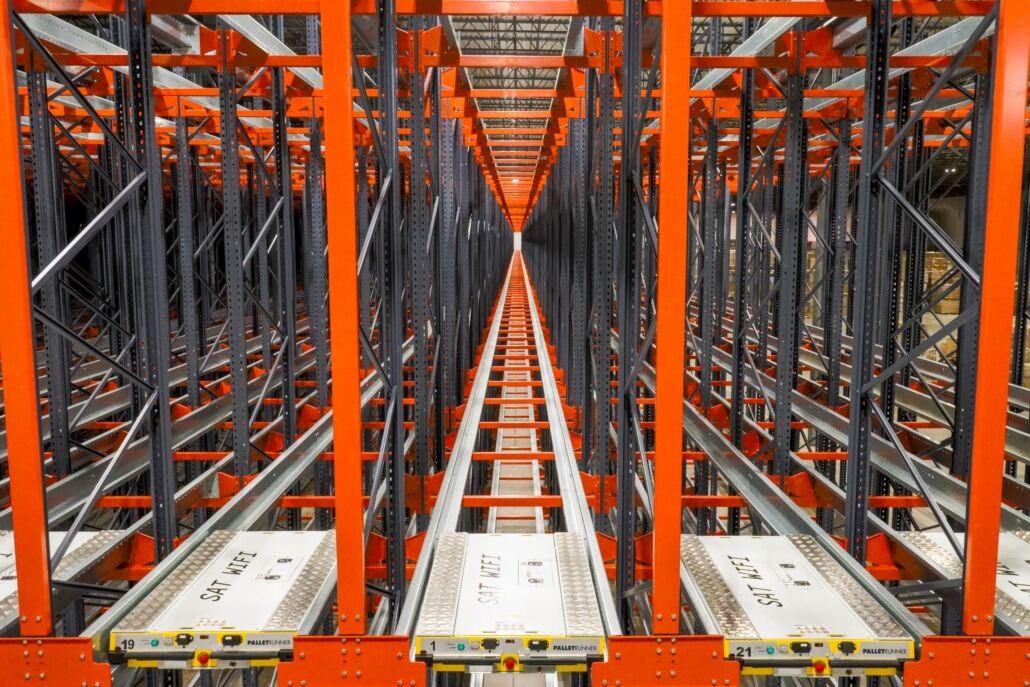
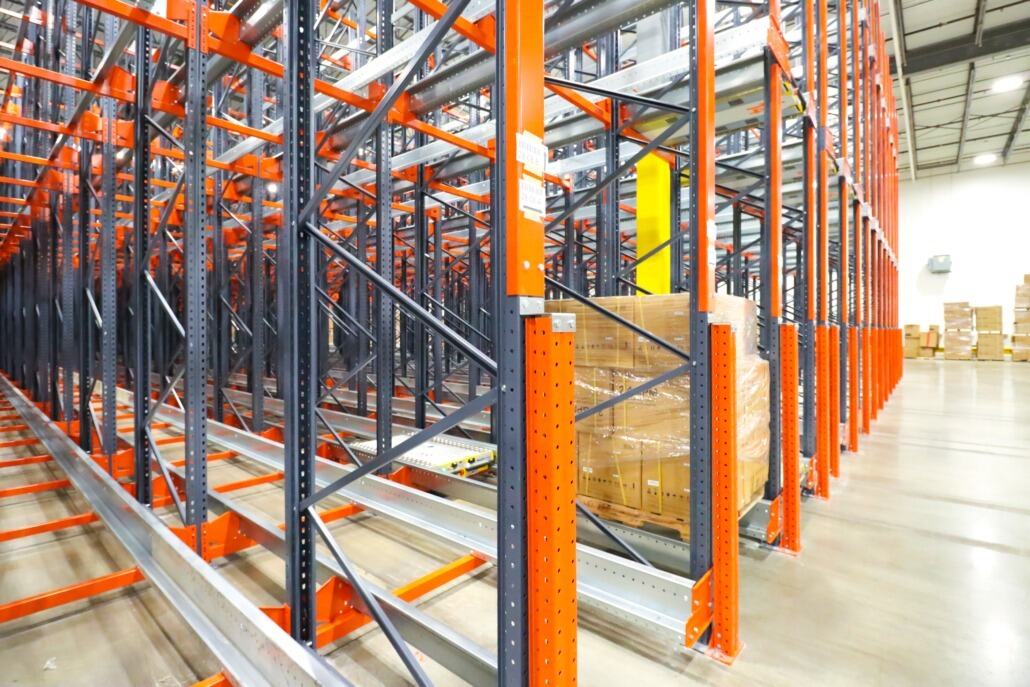
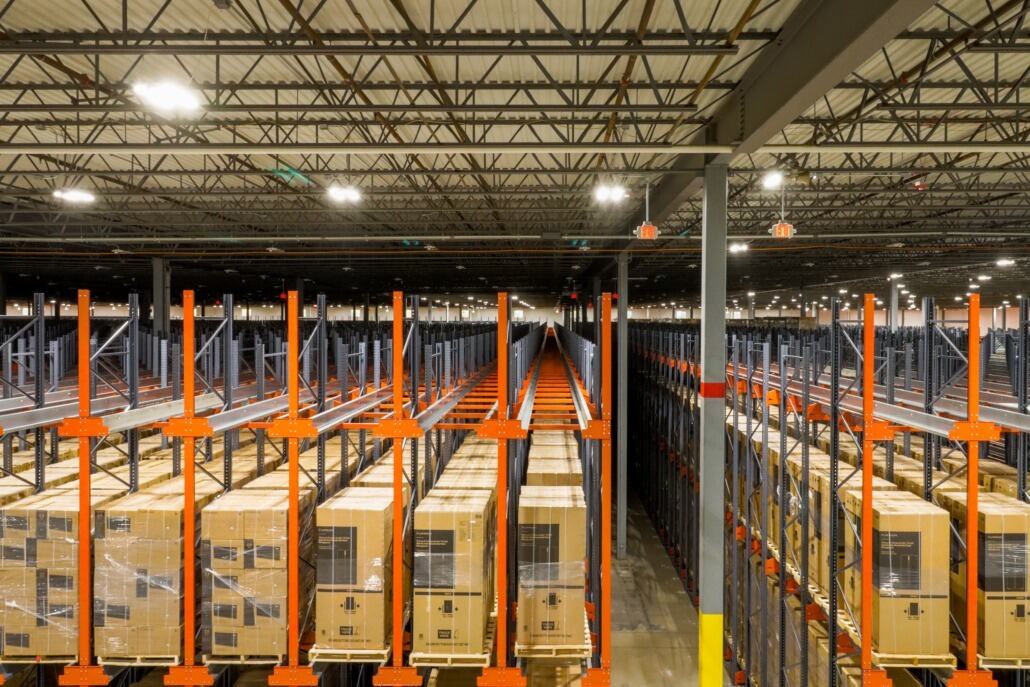
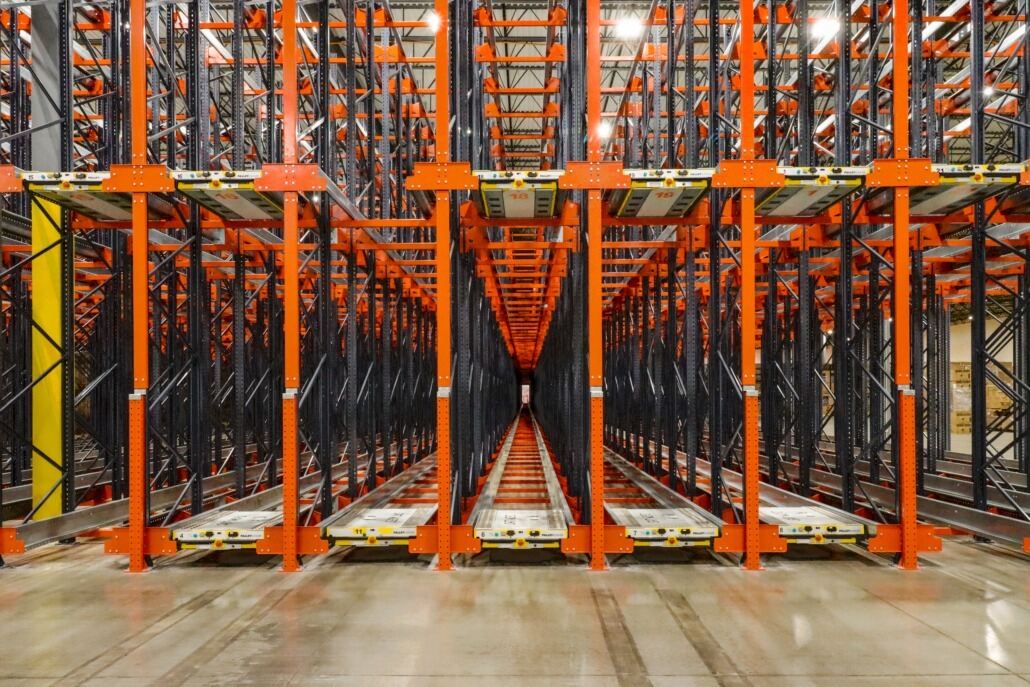
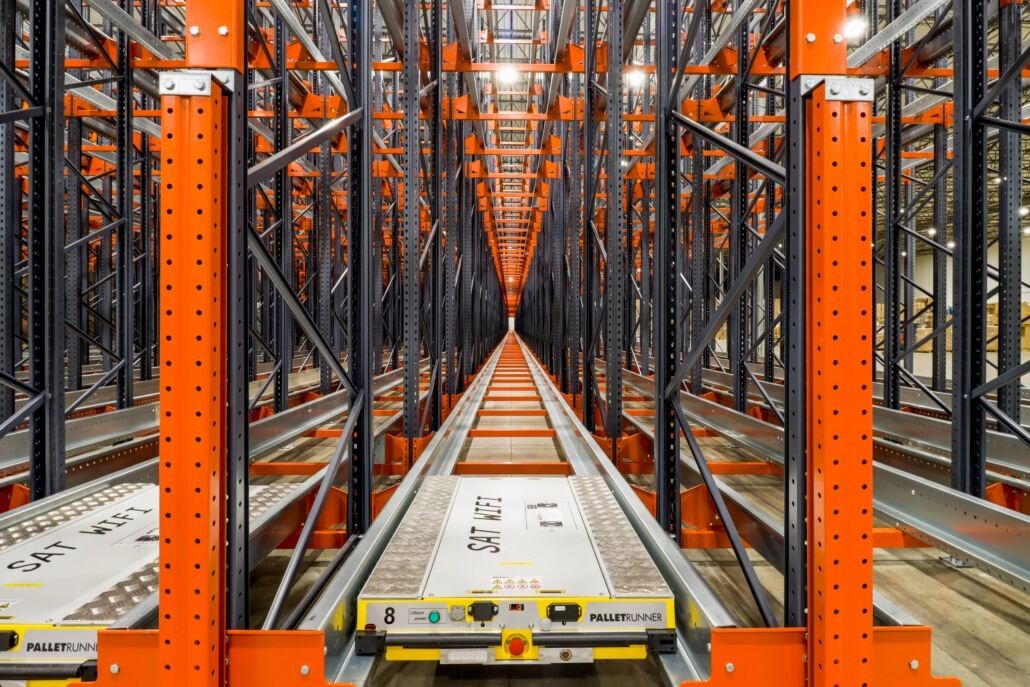
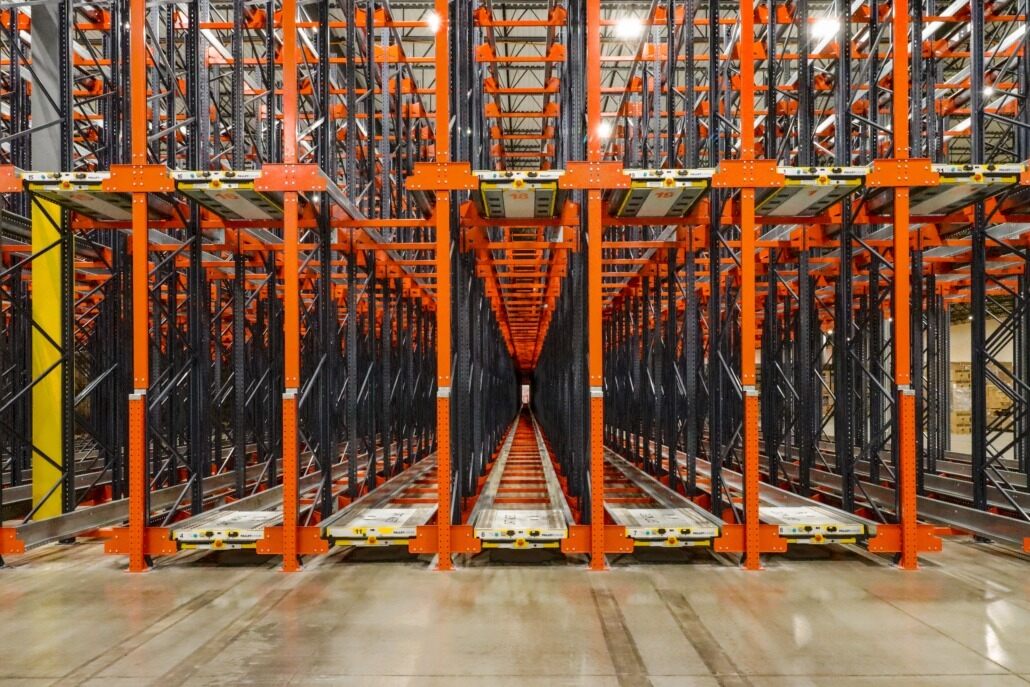





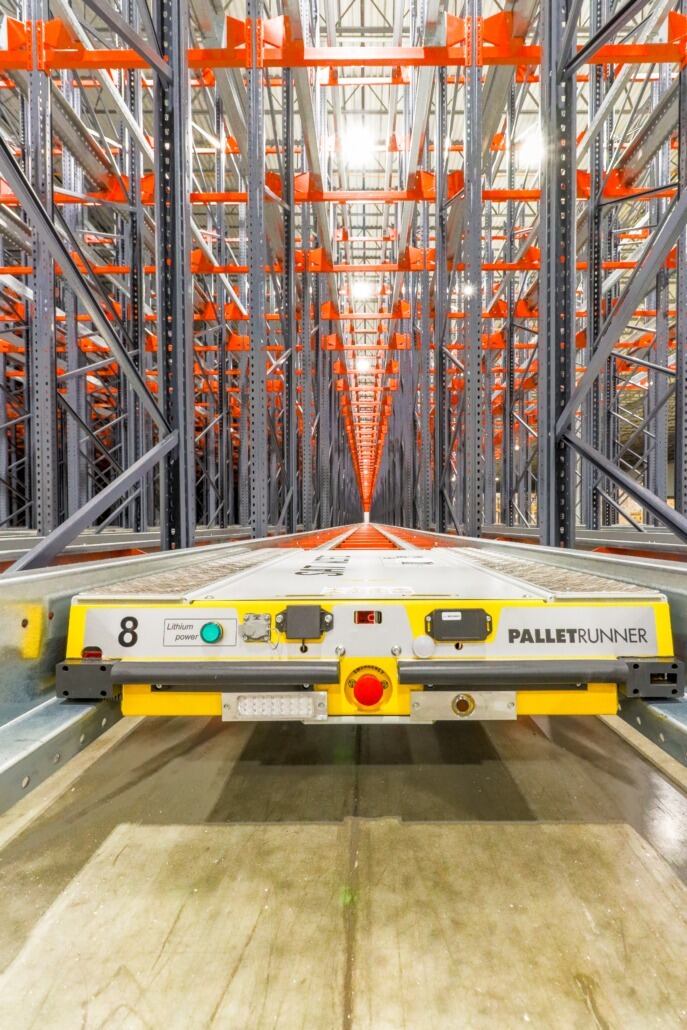
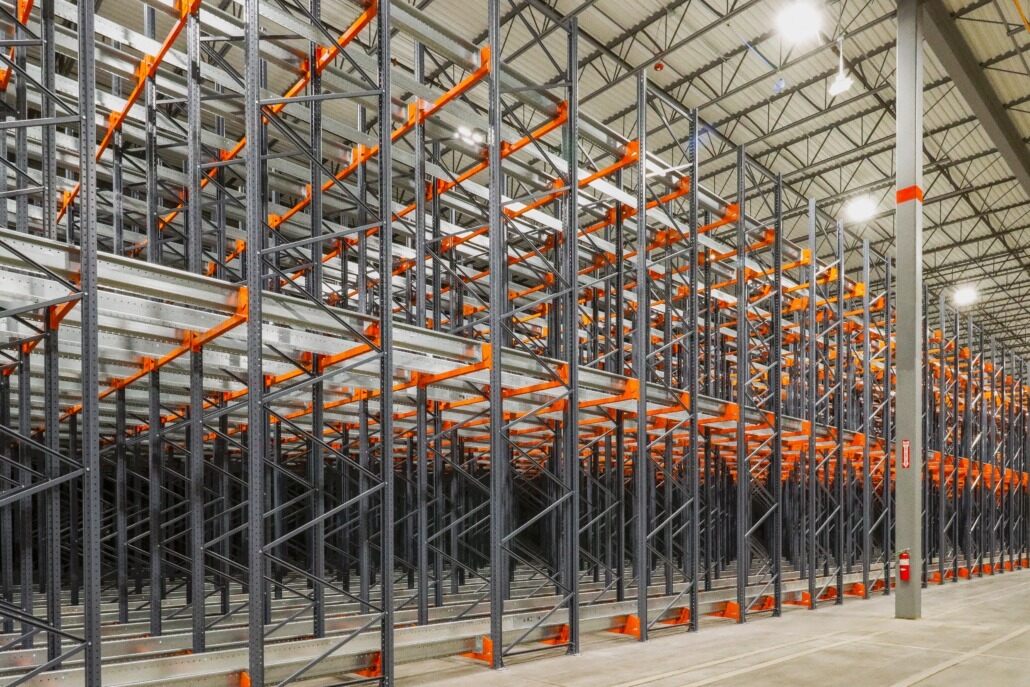


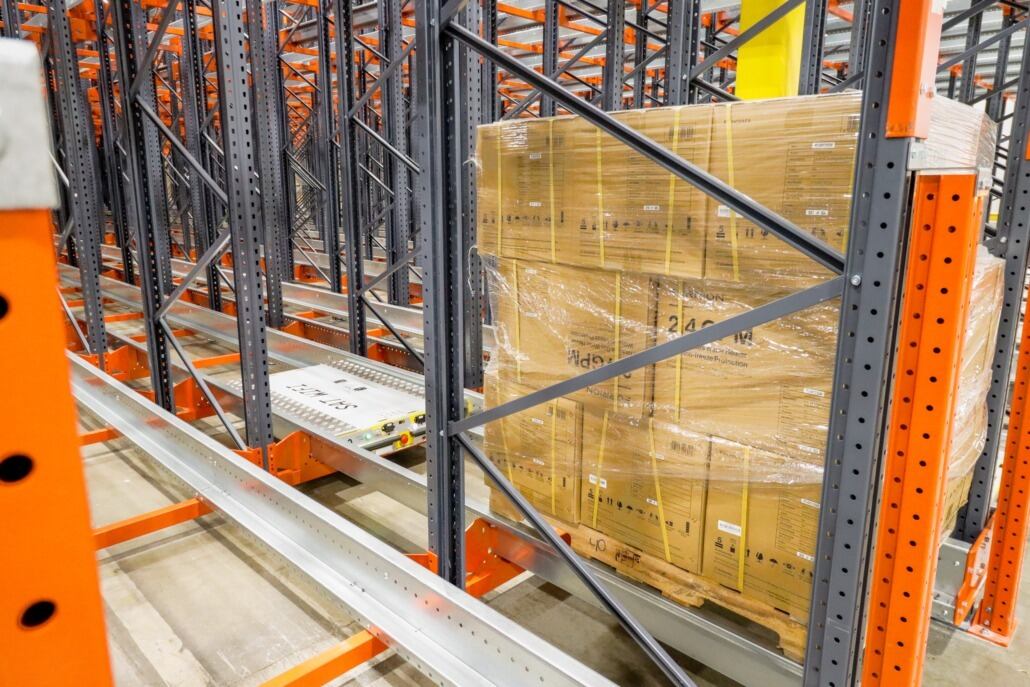




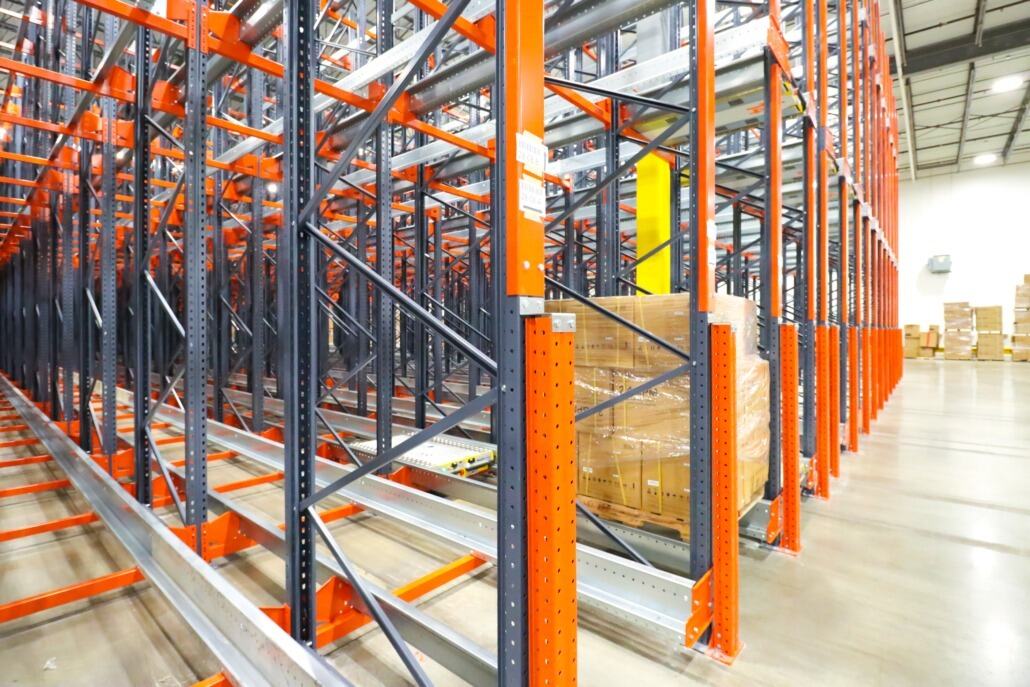